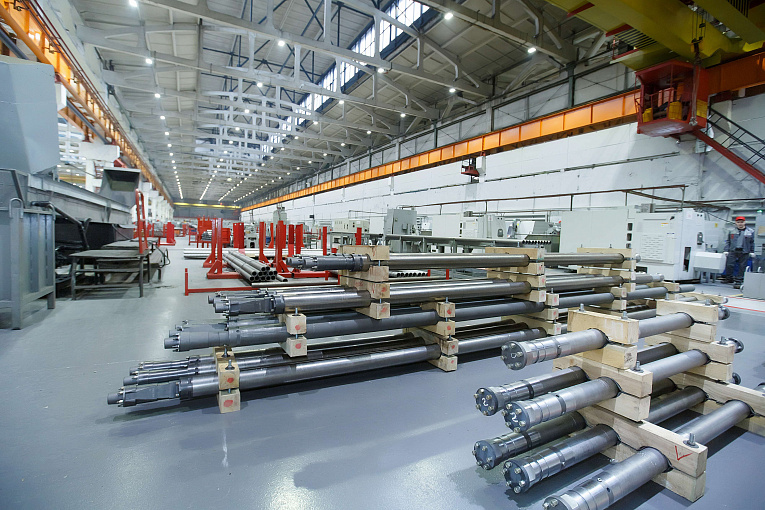
30 ноября 2020
1248
30 ноября 2020
1248
("Нефть. Газ. Новации", №7/2020) Проведен анализ существующих стендов и методик испытания газосепараторов установок погружных электроцентробежных насосов для добычи нефти, представлена новая методика и пневмогидравлическая схема стенда, разработанные с учетом замечаний и предложений по изменению существующих исследовательских стендов.
Авторы: А.В. Трулев, к.т.н. /АО «Римера», г. Москва/, С.Ф. Тимушев, д.т.н., проф. /ФГБОУ ВО «Московский авиационный институт (национальный исследовательский университет)», г. Москва/, Е.М. Шмидт /ИЦ ООО «Алнас», г. Альметьевск/.
В настоящее время более двух третей нефти добывается установками погружных электроцентробежных насосов (УЭЦН). Одним из основных способов интенсификации добычи и повышения коэффициента извлечения нефти (КИН) является повышение депрессии на пласт путем снижения забойного давления. При наличии свободного газа заметно снижаются эффективность работы погружного насосного оборудования, КПД и напор насосов. В нефтедобывающих скважинах с высоким содержанием свободного газа повышение эффективности работы центробежных насосов (ЭЦН) достигается путем комплектации их центробежными газосепараторами, в которых до поступления на вход насоса у перекачиваемой среды большая часть свободного газа отбирается и отводится в затрубное пространство скважины.
Центробежные газосепараторы являются важным элементом насосной установки, одним из основных способов защиты УЭЦН от вредного влияния свободного газа. В этой связи актуальной задачей является проведение корректных стендовых испытаний газосепараторов как неотъемлемой части мероприятий, направленных на совершенствование их конструкции. Стенды для испытания сепараторов появились практически у всех ведущих производителей погружных установок. Однако, по мнению авторов, до сих пор нет общепризнанной методики испытаний сепараторов на эффективность отделения газа
и стенда для ее реализации. Конструкции газосепараторов создаются путем экспериментальной проверки новых идей и технических решений, поэтому улучшение методики испытаний должно повлиять в лучшую сторону на конструкцию сепараторов.
Авторы настоящей статьи представляют краткий анализ существующих стендов и методик испытаний и разработанный на его основе вариант новой концептуальной методики и пневмогидравлической схемы (ПГС) стенда, которые отличаются относительной простотой и надежностью.
ДВЕ ОСНОВНЫЕ МЕТОДИКИ СТЕНДОВЫХ ИССЛЕДОВАНИЙ НА ЭФФЕКТИВНОСТЬ СЕПАРАЦИИ ГАЗА
Можно выделить две основные методики испытаний газосепараторов на эффективность отделения свободного газа и, соответственно, две ПГС стендов для реализации этих методик:
Газосепаратор установлен в трубе, которая имитирует скважинную колонну, поток газожидкостной смеси подается на вход в колонну (см. принципиальную схему стенда РГУ им. И.М. Губкина, изложенную в работах [1, 2, 3, 4]). Поток ГЖС подается непосредственно на вход в газосепаратор, снаружи газосепаратора в области выходных отверстий для удаления отсепарированного газа
герметично установлен кожух, который имитирует скважинную колонну.
Можно выделить преимущества и недостатки каждой методики. В первой методике
наиболее полно и точно имитируется работа газосепаратора в скважине, поэтому
может быть получена интегральная характеристика. Сепарация газа складывается из
двух составляющих:
– сепарация газа на входе основания (часть газа, проходящая мимо входа в
газосепаратор);
– принудительная сепарация (внутри газосепаратора).
Для совершенствования проточной части необходимо определить эффективность
принудительной сепарации газа в газосепараторе. Эффективность принудительной
сепарации газа трудно вычленить из интегральной характеристики. Невозможно
определить, какая часть газа вошла в ГС, так как это зависит от многих факторов.
Сепарация на входе зависит от конструкции основания, входной решетки, подачи,
дисперсности ГЖС. Часть жидкости может выходить вместе с газом через отверстия
для выхода отсепарированного газа 10 и возвращаться на вход в газосепаратор. На
некоторых режимах работы часть жидкости может поступать внутрь через отверстия
для отвода газа.
Во второй методике преимуществом является то, что газожидкостная смесь подается
непосредственно на вход испытуемого газосепаратора. Таким образом, может быть
получена информация по эффективности отделения свободного газа внутри ГС,
которая помогает оценить работу элементов проточной части. Недостатком является
то, что необходимо искусственно поддерживать разницу давлений на входе в
газосепаратор и снаружи, в области отверстий, для выхода отсепарированного газа
10, что можно сделать лишь с некоторой погрешностью. В этой методике не
учитывается эффективность работы подводящих и отводящих каналов основания и
головки сепаратора. Возникают трудности также с моделированием эффекта
поступления жидкости снаружи в каналы для отвода газа.
АНАЛИЗ ПЕРВОЙ МЕТОДИКИ И СТЕНДА ДЛЯ ЕЕ РЕАЛИЗАЦИИ
Принципиальная схема стенда РГУ им. И.М. Губкина изложена в работах [3, 4, 6, 7].
В качестве модельной жидкости используется вода с добавлением в нее
поверхностно-активного вещества (ПАВ) Dissolvan-4411 с объемной концентрацией
0,05 %. Вода поступает из емкости в подпорный насос, представляющий собой
секцию погружного насоса. Высоконапорная жидкость после насоса используется в
качестве активного потока эжектора, сопло которого выбирается из условий
критического течения потока в нем при заданном расходе Qнач и давлении перед
соплом Р=2 МПа (20 кгс/см2). В результате этого:
подача жидкости Qнач при неизменном сопле остается постоянной вне зависимости
от газосодержания в потоке bвх = Qr/Qcm в гидравлической системе, где Qcm –
объемный расход газожидкостной смеси;
в сечении эжектора сразу за соплом имеет место глубокий вакуум, позволяющий
атмосферному воздуху поступать в эжектор перед камерой смешения.
В эжекторе в камере смешения происходит дробление, диспергирование газа.
Газожидкостная смесь после эжектора поступает в «модель» скважины, в которой
установлены газосепаратор и секция погружного насоса, состоящая приблизительно
из 12 ступеней. В газосепараторе большая часть газа сепарируется и отводится в
модель скважины. Дегазированная жидкость с частично оставшимся газом через
магистраль сбрасывается снова в бак.
Можно выявить следующие недостатки:
Эжектор, установленный на входе в колонну, имеет сменные сопла, то есть подачу
можно менять только дискретно. При установленном сопле подача жидкости не
меняется, испытания проходят при установленной начальной подаче жидкости, на
которую настроен расход газосепаратора. Подача газа увеличивает расход
газожидкостной смеси. При гасодержании свободного газа на входе в 50 % подача
ГЖС на входе в колонну в два раза превосходит начальную подачу жидкости, а при
содержании 70 % – в три раза. Вся избыточная подача протекает мимо
газосепаратора. Происходит имитация работы в фонтанирующей скважине, в которой
установки ЭЦН обычно не используются. Нарушаются условия течения потока на
входе в газосепаратор и в области отверстий для выхода газа. С учетом того, что
подача самого сепаратора снижается при работе на ГЖС, скорость фонтанирования
потока увеличивается.
Испытывается установка в составе газосепаратора и установленного на выходе
погружного насоса, в состав которого входит 12 ступеней с оптимальной подачей,
примерно совпадающей с подачей газосепаратора. Но работа такого насоса очень
чувствительна к дисперсности ГЖС и к давлению на входе. Соответственно,
диспергирующие устройства и элементы, установленные в головке ГС и на его
выходе, заметно меняют работу установки. В этих условиях, как показано в статьях [1,
2], сходные по конструкции газосепараторы имеют разную эффективность по причине
установки на выходе одного из них диспергирующего элемента. Подачи через
газосепараторы с одинаковой конструкцией могут отличаться между собой, при этом
быть заметно меньше, чем начальная подача через эжектор, за счет
диспергирующего модуля. Но именно начальная подача через эжектор указывается
на графиках для коэффициента сепарации и допустимого содержания свободного
газа на входе в насос.
Работа газосепаратора с маломощным насосом из 12 ступеней становится зависимой
от площади входных и выходных отверстий для жидкости в основании и головке
газосепаратора. В реальной скважине при работе с полноразмерным насосом из 500
ступеней, который принудительно прокачивает через газосепаратор определенный
расход газожидкостной смеси, такой зависимости нет.
На выходе из колонны установлен гравитационный сепаратор для подготовки
стендовой жидкости, эффективность работы которого на два-три порядка уступает
центробежному сепаратору, поэтому приходится несколько часов ожидать
разделения жидкой и газовой фаз для каждого измерения, а испытания одного
газосепаратора затягиваются на несколько дней.
Результатом испытаний является зависимость допустимого содержания на входе
свободного газа от начальной подачи жидкости, но при этом реальная подача
жидкости через газосепаратор, как показано в статьях [1, 2], может быть заметно
меньше. Поэтому возникает неточность в оценке эффективности работы изделия.
Несмотря на недостатки, данная методика и стенд позволяют сравнивать подобные
конструкции газосепараторов, результатам таких испытаний можно доверять.
Однако при испытаниях газосепаратора и этого же газосепаратора с установленным
на выходе диспергирующим модулем по этой методике будут получены разные
показатели эффективности сепарации газа. Это свидетельствует о недостатках
стенда и методики, так как никакие диспергирующие устройства, установленные на
выходе из сепаратора, не могут влиять на его работу, не меняют структуру потока
внутри ГС.
На пневмогидравлической схеме, представленной в патенте [14], устранены
вышеуказанные недостатки. Вместо эжектора на входе в колонну установлен
роторный диспергатор, подача которого может плавно меняться. Добавлено
дополнительное сепарирующее устройство, которое имитирует сепарацию ГЖС в
колонне, удаление газа и возвращение жидкости.
АНАЛИЗ ВТОРОЙ МЕТОДИКИ И СТЕНДА ДЛЯ ЕЕ РЕАЛИЗАЦИИ
Принципиальная схема стенда с дополнительным гравитационным устройством для
разделения жидкой и газообразной фаз ГЖС, вышедшей из отверстий 10 для отвода
отсепарированного газа. Стенд разработан в АО «Римера» (ООО «Алнас»), защищен
патентами [13, 15], пояснения изложены в статье [12].
Стенд содержит испытуемый газосепаратор 1 с основанием 2 и выкидными
отверстиями 3 в головке, а также линию отвода отсепарированной жидкости 4, линии
подвода жидкости 5 и газа 6, которые объединяются в линию подвода газожидкостной
смеси, выполненную в виде входного модуля с диспергатором 7.
Головка (выход) диспергатора 7 во время испытаний газосепаратора 1 соединена с
основанием газосепаратора 2. Снаружи выкидных отверстий 3 установлен кожух 8
герметично по отношению к газосепаратору 1.
Кожух 8 соединен трубопроводом 9 со входом в дополнительное устройство для
сепарации жидкости и газа 10.
Линия для отвода отсепарированного газа 12 соединена с атмосферой.
Следует отметить, что площадь сечения трубопровода линии 9 должна быть
сравнима с суммарной площадью отверстий для выхода газа в головке ГС, в
противном случае уменьшится расход отсепарированного газа и ГЖС по сравнению с
ГС в скважине без линии 9.
В линии 9 установлен регулирующий клапан КР3, который поддерживает заданное
значение давления в кожухе. Жидкость (вода), циркулирующая в стенде, содержится
в баке 14.
Расходы жидкости и газа, которые поступают в газосепаратор, измеряются
расходомерами РМ1 и РМ2. ГЖС, вышедшая из отверстий отвода отсепарированного
газа 3, через кожух 8 и линию 9 поступает в гравитационное сепарирующее
устройство, основным элементом которого является мерный бак 10. Объем газа,
который выходит из бака 10, измеряется газовым счетчиком РМ3. Объем жидкости
измеряется шкалой мерного бака 10.
Приводом для установки с газосепаратором 1 является двигатель 13.
На выходе из газосепаратора 1 может быть установлена пустая труба 15, чтобы
вписаться в стандартные габариты горизонтального стенда. Выход из газосепаратора
1 через линию отвода отсепарированной жидкости 4 соединен с баком 14. Если
площадь свободной поверхности бака 14 недостаточна для сепарации ГЖС, на
выходе линии 4 может быть установлено сепарирующее устройство, например в виде
полочного сепаратора.
При испытании газосепараторов на эффективность отделения газа не следует
устанавливать на его выходе насосную секцию, диспергатор, мультифазные модули,
так как они могут являться дополнительными гидравлическими сопротивлениями, для
преодоления которых придется повышать давление на входе в газосепаратор.
Подача через газосепаратор 1 должна задаваться регулирующим клапаном КР4.
Давление и температура на входе в диспергатор 7 измеряются манометром МН,
термометром Т, на входе в газосепаратор 1 – МН1, Т1, в кожухе 8 – МН2, Т2, на
выходе из газосепаратора – МН4, Т4, в линии 12 – МН3, Т3.
Никакие устройства, установленные на выходе из азосепаратора, например
диспергаторы, не могут влиять на сепарационные свойства газосепаратора, поэтому
нет смысла в их установке.
Давление в зоне отверстий для выхода газа должно задаваться и поддерживаться
равным давлению на входе в ГС минус вес столба ГЖС высотой от входа до
отверстий для выхода газа.
Целесообразно замерить давление экспериментально до испытаний газосепаратора,
установив на его место муляж в виде пустой трубы, которая будет имитировать
обсадную колонну, затрубное пространство, и замерять давление в зоне
предполагаемого входа в ГС и в зоне отверстий для выхода газа при различных
подачах жидкости и объемных газосодержаниях потока смеси. Это даст реальный
перепад давлений, который должен поддерживаться при стендовых испытаниях.
Величина (рис. 1) определяет объемное газосодержание потока в смеси.
В случае если имеются трудности с экспериментальным замером давлений, можно
сделать расчетпо формуле (рис. 2).
P1 – давление на входе в газосепаратор, измеренное манометром 30;
P2 – давление в зоне отверстий для выхода газа, измеренное манометром 32.
Плотность смеси (рис. 3)
Величина представляет собой мгновенное значение доли сечения потока, занятого
газовой фазой, т.е. истинное газосодержание смеси [10, 11];
S – площадь сечения канала, Sг – площадь, занятая газовой фазой.
В связи с тем, что скорость движения газовой фазы при движении потока ГЖС вверх
больше скорости движения жидкости, плотность будет выше по сравнению с
вариантом, при котором скорости движения фаз одинаковы. Разница учитывается
увеличивающим коэффициентом k, значение которого зависит от диаметра
пузырьков газа, градиента давления, плотности и т. д.
ρсм, ρг, ρж – плотности смеси, газа и жидкости, приведенные к давлению на входе в
газосепаратор, замеренному манометром 30;
Qг, Qж – подачи газа и жидкости на вход в газосепаратор, замеренные расходомерами
15 и 16 и приведенные к давлению на входе в газосепаратор;
hc – расстояние меду входом в газосепаратор и отверстиями для выхода газа;
cosα – косинус угла между осью газосепаратора и вертикальной осью;
hc · cosα – разница по высоте между отверстиями для входа и выхода газа с учетом
отклонения установки газосепаратора от вертикали.
Увеличивающий коэффициент k лучше определить экспериментально, замерив
предварительно давление по методу, описанному выше.
При объемном содержании газа, равном 50 %, его значение может находиться в
пределах от 1 до 2. Для эксперимента в первом приближении можно принять
коэффициент k равным 1,5.
Давление P2 регулируется клапаном 13 по показаниям манометра 32.
Таким образом, при испытаниях на горизонтальном стенде можно имитировать
работу газосепаратора при любых углах установки его в скважине.
Стендовые испытания, моделирующие работу сепаратора в горизонтальной
скважине, представлены в патенте [15]. В этом случае выход трубопровода линии 11
можно соединить напрямую с линией 5.
Расход отсепарированного воздуха, вышедшего из бака 10, определяется как объем
воздуха, вышедшего из бака 10 за некоторый интервал времени, минус объем
жидкости, оставшейся в этом баке, деленный на этот интервал времени (рис. 5):
– объемы отсепарированных газа и жидкости за интервал времени t.
ПОРЯДОК ИСПЫТАНИЙ
Перед испытаниями начальное состояние всех вентилей, кранов и клапанов –
закрытое; электроприводы насоса Н газосепаратора ГС не включены. Испытания
проводятся в следующем порядке.
1. Открываются запорные клапаны в линии подвода воды. Включаются насос 17 и
электродвигатель 13, приводящий в действие газосепаратор 1 и диспергатор 7.
2. Открытием регулирующего клапана КР4 устанавливается подача жидкости в
газосепаратор, соответствующая примерно 1/N максимального запланированного
расхода, где N – количество снимаемых экспериментально точек. Измеряются
давление и подача жидкости.
3. Трехходовой клапан КТ1 гидравлически соединяет линию 9 с баком 14. Открытием
регулирующего клапана КР2 устанавливается подача газа на величину примерно 1/М
от максимального запланированного расхода, где М – количество снимаемых
экспериментально точек. Воздух поступает в диспергатор 7, образуется ГЖС.
4. Регулирующим клапаном КР3 устанавливается требуемая разница давлений между
входом в газосепаратор и затрубным пространством в области отверстий для выхода
газа в соответствии с формулой (рис. 1).
5. Для поддержания постоянного расхода жидкости на выходе из ГС следует при
необходимости клапаном КР1 изменить давление на входе в ГС. При этом нужно
обеспечивать требуемую разницу давлений по п. 3.
6. После достижения установившегося режима работы следует трехходовым краном
КТ1 соединить линию 9 с мерным баком 10. Расходомерами РМ1, РМ2 замеряется
подача на входе в установку жидкости и газа; газовым счетчиком РМ3 – объем
отсепарированного газа, шкалой мерного бака 9 – расход жидкости, вышедшей через
отверстия для отвода газа 3. Расход отсепарированного воздуха рассчитывается по
формуле (4).
7. Регулирующим клапаном КР2 устанавливается подача газа на величину примерно
2/М от максимального запланированного расхода воздуха, и процедура измерений
повторяется (с пункта 3); и так до достижения максимального запланированного
расхода воздуха.
8. Затем регулировкой клапана КР4 устанавливается подача жидкости,
соответствующая примерно 2/N максимального запланированного расхода, и
процедура измерений повторяется (с пункта 2); и так – до достижения максимального
запланированного расхода жидкости.
Общее количество экспериментов равно N*M.
Еще раз отметим, что работа газосепаратора правильно моделируется в скважине за
счет того, что:
Перепад давлений на входе в газосепаратор и на выходе из отверстий для отвода
отсепарированного газа, измеряемого манометрами МН2 и МН1, поддерживается
равным перепаду давлений в этих точках в реальной скважине.
При испытаниях с различным содержанием свободного газа расход жидкости на
выходе из ГС поддерживается неизменным и равным расходу, который
устанавливается регулирующим клапаном КР4 до начала подачи газа.
При этом измеряется вся необходимая информация для расчета коэффициента
сепарации, объемного содержания свободного газа на входе в газосепаратор и насос.
Вторая принципиальная схема стенда РГУ им. И.М. Губкина, представленная в
работе [5]. Ее отличие состоит в том, что от кожуха, окружающего выкидные
отверстия, отходит только один трубопровод для отвода газа.
Основным параметром, определяющим эффективность сепарации газа в вихревых
газосепараторах, является радиальный градиент давления на выходе из
сепарационной камеры. Он определяется как разница между давлением на
периферии и в центре сепарационной камеры 9. Чем выше этот перепад давления,
тем с большей скоростью пузырьки газа движутся от периферии к центру.
Периферия сепарационной камеры 9 гидравлически связана с выходом из
газосепаратора 12 через отверстия 10 для отвода дегазированной жидкости в головке
3. Давление на выходе 12 из ГС равно давлению на периферии сепарационной
камеры 9 за вычетом гидравлических потерь в отверстиях 10 головки, оно
определяется манометром при определенной подаче, которая должна задаваться
клапаном, установленным на выходе из ГС.
Центр сепарационной камеры гидравлически связан с выкидными отверстиями в
головке каналами для отвода газа 11. Давление на выходе из выкидных отверстий
должно задаваться согласно (1).
Анализ испытаний газосепараторов, представленных в отчете [5], показывает, что оба
эти давления задаются некорректно.
ЗАМЕЧАНИЯ И РЕКОМЕНДАЦИИ ПО МЕТОДИКЕ И СХЕМЕ СТЕНДА
По отчету [5] можно сделать следующие замечания.
При определении сепарирующих свойств газосепаратор на всех режимах работает на
открытую задвижку. Изменение подачи жидкости и газа осуществляется за счет
клапанов, установленных на входе, или за счет изменения числа оборотов насоса,
подающего воду на вход в газосепаратор. В этом случае структура потока в ГС не
соответствует действительному течению. В реальной скважине на выходе из ГС
установлен насос с фиксированной подачей. Давление на выходе из газосепаратора
12 гидравлически, через каналы 10 в головке 3, связано с давлением на периферии
сепарационной камеры 9 и отличается на величину гидравлических потерь в каналах
10.
На стенде затрубное пространство имитирует атмосфера. Именно за счет того, что
давление ГЖС на периферии сепарационной камеры выше, чем давление в
затрубном пространстве, осуществляется сепарация газа в затрубное пространство
[18, 19], на стенде – в атмосферу. При испытаниях на открытую задвижку давление на
периферии сепарационной камеры, по сути, приравнивается к давлению в затрубном
пространстве, соответственно на стенде – к атмосферному давлению. Это приводит к
нарушению условий работы, снижению давления на периферии сепарационной
камеры и градиента давления в радиальном направлении, за счет которого и
происходит сепарация газа, т. е. к ухудшению сепарирующих свойств. Сложно
выдавливать газ в атмосферу из сепарационной камеры, в которой давление –
атмосферное.
В газосепараторе течет двухфазный поток, газожидкостная смесь, там уже
изначально отсутствует сплошная жидкая среда. Поэтому согласно рекомендациям
ГОСТ Р 56830-2015 на испытания ГС подача воды должна задаваться задвижкой на
выходе. Этот вопрос также раскрывается в [7, 8, 9, 17] и в ГОСТ 6134-2007 «Насосы
динамические. Методы испытаний».
Работой при открытой задвижке можно объяснить тот факт, что коэффициент
сепарации при повышении скорости вращения ротора в отчете [5] не увеличивается,
так не увеличивается давление на выходе из ГС, которое на всех режимах работы
равно давлению атмосферы и отличается лишь на величину гидравлических потерь.
Замечание о том, что газосепаратор нельзя испытывать при открытой задвижке,
относится и к его испытаниям на износо-стойкость.При определении сепарирующих
свойств не правильно назначается давление в области отверстий для выхода
отсепарированного газа, поэтому неточно моделируется работа газосепаратора в
скважине. Перепад давления между входом в ГС и областью отверстий для выхода
отсепарированного газа должен задаваться согласно уравнению (1), быть таким же,
как в скважине, равным весу столба
ГЖС, высота которого равна расстоянию между входом и выкидными отверстиями
[20].
Отсутствует устройство для сепарации и линия отвода жидкости из области выкидных
отверстий для газа. Площадь трубопровода, отводящего отсепарированный газ и
ГЖС, на порядок меньше, чем суммарная площадь отверстий для выхода газа в
головке ГС.
Литература
1. Деньгаев А.В., Дроздов А.Н., Вербицкий В.С. Испытания газосепараторов габарита
5А к центробежным электронасосам // Нефтяное хозяйство. – 2004. – № 6. – C. 96–99.
2. Стендовые испытания газосепараторов к погружным центробежным насосам / Л.В.
Игревский, А.Н. Дроздов, А.В. Деньгаев, Д.Н. Ламбин // Нефтепромысловое дело. –
2002. – № 9. – С. 28–32.
3. Отчет о НИР по договору № 80-12/05-01-12 от 15.02.2012 по теме «Разработка
газосепаратора в габарите 5 со сменными шнеками». – М.: РГУ нефти и газа им. И.М.
Губкина, 2015. – 159 с.
4. Информационный отчет по теме договора №113-УК/61-07 от 14.10.2007
«Обоснование и разработка рациональной ПГС стенда для экспериментальных
исследований характеристики газосепараторов». – М.: РГУ нефти и газа им. И.М.
Губкина, 2007. – 80 с.
5. Отчет по договору № АЛН-ДВОУПТ/0996/18 от 19.12.2018 по теме «Стендовые
испытания газосепаратора и газосепаратора – диспергатора 4 габарита». – М.: РГУ
нефти и газа им. И.М. Губкина, 2018. – 63 с.
6. Миронов Ю.С., Гафуров О.Г., Асылгареев А.Н. Особенности совместной работы
ступеней погружного электроцентробежного насоса при откачке газожидкостной
смеси // Сб. аспирантских работ УФНИИ. – 1970. – Вып. IV. – С. 146–168.
7. Рахматуллин Ш.И. Кавитация в гидравлических системах магистральных
нефтепроводов. – М.: Недра, 1986. – 165 с.
8. Колпаков Л.Г., Рахматуллин Ш.И. Кавитация в центробежных насосах при
перекачке нефти и нефтепродуктов. – М.: Недра, 1986. – 164 с.
9. Яременко О.В. Испытания насосов. – М.: Машиностроение,1976. – 222 с.
10. Кутателадзе С.С., Стырикович М.А. Гидравлика газожидкостных систем. – М.-Л.:
Госэнергоиздат, 1958. – 231 с.
11. Тонг Л. Теплоотдача при кипении и двухфазное течение. – М.: Мир, 1963. – 342 с.
12. Исаев Г.А., Калан В.А., Петров В.И. Проектная разработка исследовательского
стенда для испытаний газосепараторов погружных насосных установок для добычи
нефти // «СИНТ 2009» Разработка, производство и эксплуатация турбо-, электро-
насосных агрегатов и систем на их основе: тр. V Междунар.
науч.-техн. конференции. – Воронеж, 2009. – С. 136–147.
13. Патент РФ № 2425254 Стенд гидравлических испытаний газосепараторов
насосных установок для подачи пластовой жидкости / Исаев Г.А., Калан В.А., Петров
В.И., Трулев А.В. Приоритет 18.09.2009.
14. Патент РФ № 2588332 Стенд для испытания газосепараторов к погружным
электронасосным агрегатам / Трулев А.В., Ситников В.И. Приоритет 21.07.2015.
15. Патент РФ № 2647175 Способ испытаний газосепараторов на газожидкостных
смесях и стенд для его осуществления / Трулев А.В., Леонов В.В. Приоритет
21.06.2017.
16. Дроздов А.Н. Технология и техника добычи нефти погружными насосами в
осложненных условиях. – М.: МАКС Пресс, 2008. – 309 с.
17. Петров В.И., Чебаевский В.Ф. Кавитация в высокооборотных лопастных насосах. –
М.: Машиностроение, 1982. – 192 с.
18. Проблемы разработки месторождений тяжелых нефтей со сложными
геологическими условиями и пути их решения /
Трулев А.В., Тимушев С.Ф., Ломакин В.О., Каюда М.С. // Нефть. Газ. Новации. – 2020.
– № 2. – С. 55-60.
19. Trulev A., Timushev S., Lomakin V. Conceptual features of improving the flow-through
parts of gas separators of submersible electric pumps systems for the production of
formation fluid in order to improve the separating properties, energy efficiency and
reliability. Hydraulics, IOP Conf. Series: Materials Science and Engineering 779 (2020)
012036 IOP Publishing doi: 10.1088/1757-899X/779/1/012036.